Fabricante de interruptores diferenciales (RCCB)
VIOX es un fabricante y proveedor de RCCB para su marca. Somos la manera más rápida y más fácil de construir o promocionar su marca a través de la producción de alta calidad.
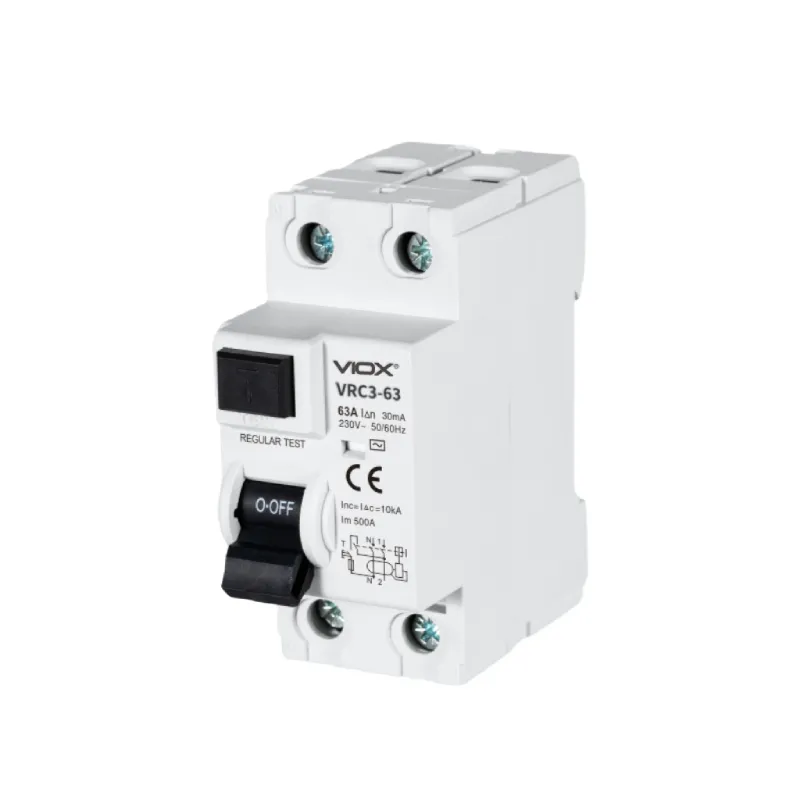
La fabricación de interruptores diferenciales (RCCB) implica un sofisticado proceso que combina ingeniería de precisión, automatización avanzada y estrictas medidas de control de calidad. Este dispositivo de seguridad crítico, diseñado para detectar fugas de corriente y evitar riesgos eléctricos, requiere un proceso de producción en varias fases que equilibre la complejidad técnica con el cumplimiento de la normativa en diversos mercados mundiales.
Principios básicos y componentes
La funcionalidad del RCCB gira en torno a la detección precisa de desequilibrios de corriente entre los conductores vivos y neutros, aprovechando un conjunto de transformadores toroidales para supervisar continuamente las corrientes diferenciales. Este mecanismo se adhiere a la Ley de la Corriente de Kirchhoff, garantizando que cualquier desviación del equilibrio de corriente esperado desencadena una respuesta inmediata, protegiendo contra posibles riesgos eléctricos.
Entre sus principales componentes e innovaciones figuran:
- Transformadores de corriente toroidales: Construidos con aleaciones nanocristalinas, estos transformadores mejoran la permeabilidad magnética, garantizando una detección precisa incluso de pequeñas corrientes de fuga.
- Relés de imán permanente (PMR): Calibrados con precisión para disparar dentro de un rango de 0,5IΔn a IΔn, estos relés garantizan un funcionamiento fiable en condiciones de fallo.
- Cámaras de supresión de arcos eléctricos: Diseñadas con polímeros termoestables emisores de gas, estas cámaras apagan eficazmente los arcos eléctricos, evitando daños mayores o riesgos de incendio.
Estrategias optimizadas de diseño de fabricación
Las estrategias de diseño para fabricación (DFM) en la producción de RCCB se centran en integrar los procesos de diseño y fabricación para aumentar la eficiencia, reducir los costes y mantener unos estándares de alta calidad. Aplicando principios de ingeniería concurrente, los fabricantes fomentan la colaboración entre los equipos de desarrollo de productos y los especialistas en automatización desde la fase de prototipo, lo que minimiza los rediseños y mejora la fabricabilidad.Las prácticas clave de DFM incluyen:
- Optimización de la geometría de los componentes para el montaje robotizado con tolerancias precisas de ±0,05 mm.
- Emplear arquitecturas de producto modulares que admitan configuraciones como las variantes 2P y 4P para agilizar la producción.
- Utilización de sistemas de producción adaptables con herramientas de cambio rápido y sistemas de visión para gestionar eficazmente diversas variantes de RCCB sin sacrificar la calidad.
Procesado avanzado de materiales conductores
La fabricación de componentes conductores para RCCB exige ingeniería de precisión y ciencia de materiales avanzada para garantizar la durabilidad, la seguridad y el rendimiento. Los contactos de plata-tungsteno, un elemento crítico, se fabrican mediante pulvimetalurgia con una composición de 85% de tungsteno y 15% de plata. Esta mezcla ofrece una excelente resistencia al arco y conductividad térmica. Los contactos se sinterizan a 1.200°C en una atmósfera de hidrógeno para conseguir una alta densidad y uniformidad, con una rugosidad superficial controlada por debajo de Ra 0,8μm para un rendimiento eléctrico óptimo. Los elementos térmicos bimetálicos se fabrican a partir de tiras de NiCr/Fe soldadas por láser con estrictas tolerancias de curvatura de ±0,01 mm/m para mantener unas características de respuesta térmica precisas. Las barras colectoras de cobre, fabricadas con cobre electrolítico de paso resistente (C11000), se estampan utilizando matrices progresivas para obtener una precisión dimensional constante. Los componentes de aislamiento y carcasa se moldean por inyección con materiales como la poliamida 66 rellena de vidrio (contenido 30% GF) para cumplir la norma UL94 V-0 y mezclas autoextinguibles de PC/ABS para piezas transparentes. Las técnicas de moldeo por coinyección mejoran aún más el diseño ergonómico al integrar sobremoldeo de TPE de tacto suave para las asas. Para evitar la migración de la plata en entornos húmedos, los protocolos de secado del material exigen un contenido de humedad ≤0,02%.Configuración de líneas de montaje automatizadas
Las modernas líneas de montaje RCCB utilizan células de producción modulares y tecnologías de automatización avanzadas para optimizar la precisión, la flexibilidad y la eficiencia. Estos sistemas incorporan estaciones especializadas, como alimentadores vibratorios para el suministro de material, sistemas robóticos de recogida y colocación para la manipulación de componentes, estaciones de soldadura láser para el ensamblaje por contacto, enrolladoras de muelles, unidades de atornillado con control de par, configuraciones de pruebas en circuito (ICT) y módulos de ensamblaje final.Entre las tecnologías clave figuran:
- Robots articulados de 6 ejes para una manipulación precisa.
- Sistemas de visión artificial con cámaras de alta resolución y algoritmos de aprendizaje profundo para la detección de defectos.
- Sistemas de transporte adaptables que permiten pasar rápidamente de una variante de producto a otra sin necesidad de ajustes mecánicos.
Protocolos de pruebas exhaustivos
Los exhaustivos protocolos de ensayo y aseguramiento de la calidad de los RCCB garantizan su fiabilidad y seguridad en diversas condiciones de funcionamiento. La validación en línea comienza con las pruebas de alto potencial, en las que se aplica una corriente alterna de 4 kV entre los polos durante 60 segundos, de conformidad con la cláusula 9.7 de la norma IEC 61008. Las pruebas de simulación de corriente diferencial verifican aún más el rendimiento mediante la aplicación de 0,5IΔn (15mA) durante 100ms para garantizar que no se produzcan disparos y 1IΔn (30mA) durante 300ms, cuando el disparo es obligatorio. Las pruebas de resistencia mecánica someten a los RCCB a 10.000 ciclos de funcionamiento con un poder de corte de 6.000 A, lo que confirma su durabilidad en condiciones de uso repetido. La certificación final del producto implica bancos de pruebas automatizados que realizan análisis de aumento de temperatura mediante termografía IR para garantizar un aumento máximo de <50K a 1,13In. Las pruebas de estrés ambiental simulan condiciones extremas, como 85°C/85% HR durante 96 horas y arranques en frío a -25°C, mientras que las pruebas de inmunidad EMC evalúan la resistencia a sobretensiones de hasta 8kV/15kV y campos RF de 10V/m de 80-1.000MHz. El control estadístico del proceso garantiza una calidad constante manteniendo un Cpk ≥1,67 a través de pruebas de producción de 100%, con un muestreo adicional a un AQL de 0,65% para mayor garantía.Selección y procesamiento de materiales
La selección y el procesamiento avanzados de los materiales desempeñan un papel crucial en la fabricación del RCCB. Los componentes conductores utilizan contactos de plata-tungsteno (85% W, 15% Ag) producidos mediante pulvimetalurgia y sinterizados a 1.200°C en atmósfera de hidrógeno, mientras que los elementos térmicos bimetálicos se crean utilizando tiras de NiCr/Fe soldadas por láser con estrictas tolerancias de curvatura. La producción de aislamientos y carcasas emplea técnicas de moldeo por inyección con materiales como la poliamida 66 rellena de vidrio (contenido 30% GF) para el cumplimiento de la norma UL94 V-0 y mezclas autoextinguibles de PC/ABS para botones de prueba transparentes.- Barras conductoras de cobre: Cobre electrolítico de paso duro (C11000) estampado con matrices progresivas.
- Moldeado por coinyección: Asas de doble material con sobremoldeado de TPE suave al tacto.
- Protocolos de secado del material: Aplicar un contenido de humedad ≤0,02% para evitar la migración de la plata.
- Rugosidad superficial para contactos de plata-tungsteno: Se mantiene por debajo de Ra 0,8μm.
Innovaciones en líneas de montaje automatizadas
Las modernas líneas de producción de RCCB integran sofisticadas tecnologías de automatización para garantizar la precisión y la eficiencia. Los componentes clave incluyen robots articulados de 6 ejes para manipular piezas delicadas, sistemas de visión artificial con algoritmos de aprendizaje profundo para la detección de defectos y sistemas de transporte adaptativos que cambian entre variantes de productos sin necesidad de reconfiguración mecánica. Los procesos de ensamblaje críticos implican la calibración PMR mediante bobinas magnetizadoras que aplican campos de 500-800 A/m, soldadura láser de fibra con una profundidad de penetración de 0,3 mm y una precisión posicional <5μm, y procesos de sellado que utilizan adhesivos de curado UV aplicados a través de boquillas de 0,2 mm. Estas técnicas avanzadas permiten a los fabricantes producir RCCB con gran precisión y uniformidad, cumpliendo estrictas normas de seguridad y rendimiento.Garantía de calidad y pruebas
Los exhaustivos protocolos de prueba y garantía de calidad forman parte integral de la fabricación de RCCB. La validación en línea incluye pruebas de alto potencial a 4kV CA durante 60 segundos, simulación de corriente diferencial con aplicaciones de 0,5IΔn (15mA) y 1IΔn (30mA), y pruebas de resistencia mecánica de 10.000 ciclos operativos a 6.000A de capacidad de ruptura. La certificación final del producto incluye bancos de pruebas automatizados que realizan análisis de aumento de temperatura, pruebas de estrés ambiental en condiciones extremas y comprobaciones de inmunidad CEM. El control estadístico del proceso mantiene un Cpk ≥1,67 a través de pruebas de producción de 100% con un muestreo AQL adicional de 0,65% para garantizar la calidad. La termografía IR verifica un aumento de temperatura <50K a 1,13In, mientras que las pruebas de inmunidad EMC incluyen resistencia a sobretensiones de 8kV/15kV e inmunidad de campo RF de 10V/m. Las pruebas de estrés ambiental incluyen 85°C/85% HR durante 96 horas y capacidad de arranque en frío a -25°C.Ventajas de la fabricación china
El dominio de China en la fabricación de RCCB se debe a su avanzado ecosistema de fabricación y a sus inversiones estratégicas en automatización. El país cuenta con un ecosistema de piezas y componentes completo y rentable, que ofrece unas condiciones inigualables para la fabricación de productos electrónicos. Esta cadena de suministro integrada permite abastecerse rápidamente de componentes especializados, desde pantallas táctiles hasta placas de circuitos, lo que posibilita una producción eficiente y ajustes rápidos a las demandas del mercado. Las fábricas chinas han adoptado las tecnologías de la Industria 4.0, invirtiendo mucho en robótica inteligente, datos en la nube y líneas de producción automatizadas. Por ejemplo, la nueva línea de producción automatizada de disyuntores en miniatura flexibles de ABB en Pekín muestra los principios avanzados de la Industria 5.0, incorporando reconocimiento visual, tecnología de alimentación flexible y procesos impulsados por IA. Este enfoque en la automatización y la digitalización ha mejorado significativamente la estabilidad, la flexibilidad y la eficiencia de la fabricación, al tiempo que reduce los costes, lo que permite a los fabricantes chinos producir RCCB de alta calidad a precios competitivos.Ventajas del RCCB de VIOX Electric
VIOX Electric se distingue como uno de los principales fabricantes de RCCB por su compromiso con la excelencia técnica, la fiabilidad del producto y la innovación orientada al cliente. La avanzada experiencia en diseño de la empresa emplea estrategias de diseño para la fabricación (DFM), optimizando los RCCB tanto para el rendimiento como para la fabricabilidad. Su enfoque de fabricación inteligente incorpora tecnologías de vanguardia como la simulación de gemelos digitales y la trazabilidad blockchain, garantizando un control de calidad sin precedentes.Las principales ventajas de elegir VIOX Electric son:
- Capacidad de certificación multiestándar mediante instalaciones de ensayo internas acreditadas por la norma ISO 17025.
- Fiabilidad excepcional con Cpk ≥1,67 mantenida mediante pruebas de producción 100% y muestreos adicionales.
- Tiempos de respuesta rápidos, con modelos premium que alcanzan tiempos de disparo de 10 ms mediante diseños de circuito magnético optimizados.
- Sistemas de producción flexibles capaces de gestionar 71 variantes técnicas.
- Diseños especializados de doble voltaje (85-300 V) con detección automática para compatibilidad con el mercado mundial.
- Prácticas de fabricación sostenibles, incluidos procesos de refrigeración de circuito cerrado y recuperación de plata.
- Asistencia técnica completa y documentación transparente para ayudar a cumplir la normativa.
Solicitar un RCCB personalizado
VIOX RCCB se complace en ayudarle con sus requisitos de OEM y RCCB de marca privada. Ofrecemos soluciones asequibles y de alta calidad.