Fabricant de disjoncteurs à courant résiduel (RCCB)
VIOX est un fabricant et fournisseur de RCCB pour votre marque. Nous sommes le moyen le plus rapide et le plus facile de construire ou de promouvoir votre marque grâce à une production de haute qualité.
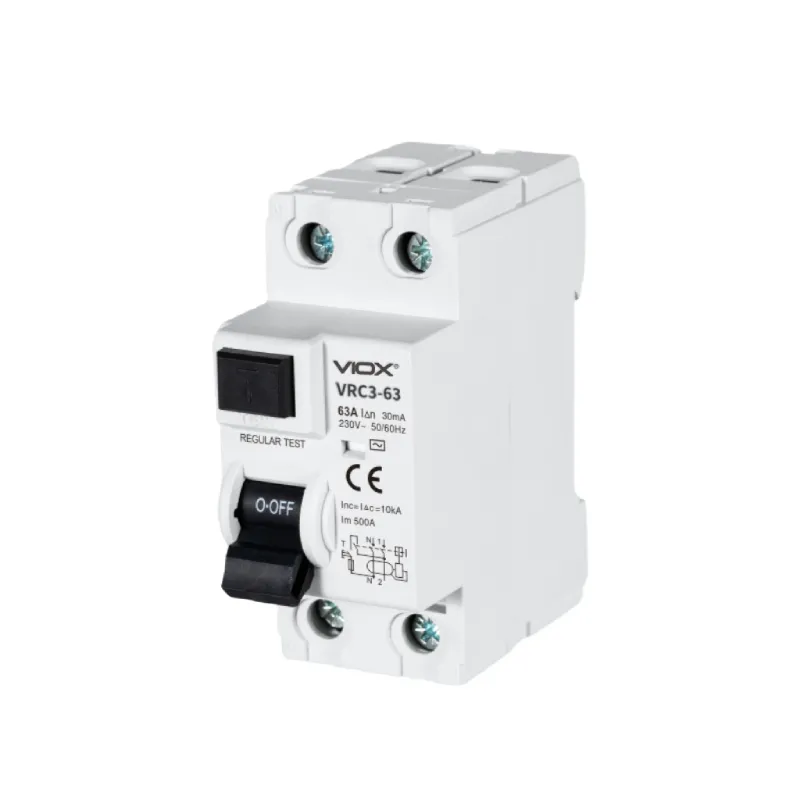
La fabrication des disjoncteurs à courant résiduel (RCCB) implique un processus sophistiqué qui combine une ingénierie de précision, une automatisation avancée et des mesures rigoureuses de contrôle de la qualité. Ce dispositif de sécurité essentiel, conçu pour détecter les fuites de courant et prévenir les risques électriques, nécessite un processus de production en plusieurs étapes qui concilie la complexité technique et la conformité réglementaire sur les différents marchés mondiaux.
Principes fondamentaux et composantes
La fonctionnalité du RCCB repose sur la détection précise des déséquilibres de courant entre les conducteurs sous tension et les conducteurs neutres, en s'appuyant sur un transformateur toroïdal qui surveille en permanence les courants différentiels. Ce mécanisme adhère à la loi du courant de Kirchhoff, garantissant que tout écart par rapport à l'équilibre attendu du courant déclenche une réponse immédiate, protégeant ainsi contre les risques électriques potentiels.
Les principales composantes et innovations sont les suivantes
- Transformateurs de courant toroïdaux : Construits avec des alliages nanocristallins, ces transformateurs améliorent la perméabilité magnétique, garantissant une détection précise des courants de fuite, même mineurs.
- Relais à aimant permanent (PMR) : Etalonnés avec précision pour se déclencher dans une plage de 0,5IΔn à IΔn, ces relais assurent un fonctionnement fiable dans des conditions de défaillance.
- Chambres de suppression d'arc : Conçues à partir de polymères thermodurcissables émettant des gaz, ces chambres éteignent efficacement les arcs électriques, évitant ainsi d'autres dommages ou risques d'incendie.
Stratégies de conception optimisée de la fabrication
Les stratégies de conception pour la fabrication (DFM) dans la production de RCCB se concentrent sur l'intégration des processus de conception et de fabrication afin d'accroître l'efficacité, de réduire les coûts et de maintenir des normes de haute qualité. En appliquant les principes de l'ingénierie simultanée, les fabricants favorisent la collaboration entre les équipes de développement de produits et les spécialistes de l'automatisation dès le stade du prototype, ce qui minimise les remaniements et améliore la fabricabilité.Les principales pratiques de DFM sont les suivantes
- Optimisation de la géométrie des composants pour l'assemblage robotique avec des tolérances précises de ±0,05 mm.
- Utiliser des architectures de produits modulaires qui prennent en charge des configurations telles que les variantes 2P et 4P afin de rationaliser la production.
- Utilisation de systèmes de production adaptatifs avec des outils à changement rapide et des systèmes de vision pour gérer efficacement diverses variantes de RCCB sans sacrifier la qualité.
Traitement avancé des matériaux conducteurs
La fabrication de composants conducteurs pour les RCCB exige une ingénierie de précision et une science des matériaux avancée pour garantir la durabilité, la sécurité et la performance. Les contacts argent-tungstène, un élément critique, sont produits par métallurgie des poudres avec une composition de tungstène 85% et d'argent 15%. Ce mélange offre une excellente résistance à l'arc et une excellente conductivité thermique. Les contacts sont frittés à 1 200 °C dans une atmosphère d'hydrogène pour obtenir une densité et une uniformité élevées, avec une rugosité de surface contrôlée en dessous de Ra 0,8μm pour des performances électriques optimales. Les éléments thermiques bimétalliques sont fabriqués à partir de bandes de NiCr/Fe soudées au laser avec des tolérances de courbure strictes de ±0,01 mm/m pour maintenir des caractéristiques de réponse thermique précises. Les barres omnibus en cuivre, fabriquées à partir de cuivre électrolytique à pas dur (C11000), sont estampées à l'aide de matrices progressives pour une précision dimensionnelle constante. Les composants d'isolation et de boîtier sont moulés par injection avec des matériaux tels que le polyamide 66 chargé de verre (30% GF content) pour la conformité UL94 V-0 et des mélanges PC/ABS auto-extinguibles pour les pièces transparentes. Les techniques de moulage par co-injection améliorent encore la conception ergonomique en intégrant un surmoulage TPE doux au toucher pour les poignées. Pour éviter la migration de l'argent dans les environnements humides, les protocoles de séchage des matériaux imposent une teneur en humidité ≤0,02%.Configuration d'une ligne d'assemblage automatisée
Les lignes d'assemblage modernes des RCCB utilisent des cellules de production modulaires et des technologies d'automatisation avancées pour optimiser la précision, la flexibilité et l'efficacité. Ces systèmes intègrent des stations spécialisées telles que des bols vibrants pour l'approvisionnement en matériaux, des systèmes robotisés de prélèvement et de placement pour la manipulation des composants, des stations de soudage au laser pour l'assemblage par contact, des machines à enrouler les ressorts, des unités de vissage à commande par couple, des installations de test en circuit (ICT) et des modules d'assemblage final.Les principales technologies sont les suivantes :
- Robots articulés à 6 axes pour une manipulation précise.
- Systèmes de vision artificielle avec caméras haute résolution et algorithmes d'apprentissage profond pour la détection des défauts.
- Systèmes de convoyage adaptatifs permettant de passer rapidement d'une variante de produit à l'autre sans ajustement mécanique.
Protocoles d'essai complets
Des protocoles complets d'essai et d'assurance qualité pour les RCCB garantissent leur fiabilité et leur sécurité dans diverses conditions opérationnelles. La validation en ligne commence par des essais à haut potentiel, où un courant alternatif de 4 kV est appliqué entre les pôles pendant 60 secondes, conformément à la clause 9.7 de la norme IEC 61008. Des essais de simulation de courant différentiel permettent de vérifier les performances en appliquant 0,5IΔn (15mA) pendant 100ms pour garantir l'absence de déclenchement et 1IΔn (30mA) pendant 300ms, lorsque le déclenchement est obligatoire. Les essais d'endurance mécanique soumettent les RCCB à 10 000 cycles de fonctionnement à un pouvoir de coupure de 6 000 A, ce qui confirme leur durabilité en cas d'utilisation répétée. La certification finale du produit implique des bancs d'essai automatisés qui analysent l'élévation de température à l'aide de la thermographie infrarouge pour garantir une élévation maximale de <50K à 1,13In. Les tests de stress environnemental simulent des conditions extrêmes, notamment 85°C/85% RH pendant 96 heures et des démarrages à froid à -25°C, tandis que les tests d'immunité CEM évaluent la résistance à des surtensions allant jusqu'à 8kV/15kV et à des champs RF de 10V/m de 80 à 1 000MHz. Le contrôle statistique des processus garantit une qualité constante en maintenant un Cpk ≥1,67 lors des tests de production à 100%, avec un échantillonnage supplémentaire à un NQA de 0,65% pour plus d'assurance.Sélection et traitement des matériaux
La sélection et le traitement avancés des matériaux jouent un rôle crucial dans la fabrication des RCCB. Les composants conducteurs utilisent des contacts argent-tungstène (85% W, 15% Ag) produits par métallurgie des poudres et frittés à 1200°C sous atmosphère d'hydrogène, tandis que les éléments thermiques bimétalliques sont créés à l'aide de bandes NiCr/Fe soudées au laser avec des tolérances de courbure strictes. La production d'isolants et de boîtiers fait appel à des techniques de moulage par injection avec des matériaux tels que le polyamide 66 chargé de verre (30% GF) pour la conformité UL94 V-0 et des mélanges PC/ABS auto-extinguibles pour les boutons d'essai transparents.- Barres omnibus en cuivre : Cuivre électrolytique à pas dur (C11000) estampé avec des matrices progressives.
- Moulage par co-injection : Poignées bi-matières avec surmoulage TPE doux au toucher.
- Protocoles de séchage des matériaux : Veiller à une teneur en humidité ≤0,02% pour éviter la migration de l'argent.
- Rugosité de surface pour les contacts argent-tungstène : Maintenue en dessous de Ra 0,8μm.
Innovations en matière de lignes d'assemblage automatisées
Les lignes de production modernes de RCCB intègrent des technologies d'automatisation sophistiquées pour garantir la précision et l'efficacité. Les principaux composants comprennent des robots articulés à 6 axes pour la manipulation des pièces délicates, des systèmes de vision industrielle avec des algorithmes d'apprentissage en profondeur pour la détection des défauts, et des systèmes de convoyage adaptatifs qui passent d'une variante de produit à l'autre sans reconfiguration mécanique. Les processus d'assemblage critiques impliquent l'étalonnage PMR à l'aide de bobines de magnétisation appliquant des champs de 500 à 800 A/m, le soudage laser à fibre avec une profondeur de pénétration de 0,3 mm et une précision de positionnement <5μm, et des processus de scellement utilisant des adhésifs durcissables aux UV appliqués à travers des buses de 0,2 mm. Ces techniques avancées permettent aux fabricants de produire des RCCB avec une grande précision et une grande cohérence, en respectant des normes de sécurité et de performance rigoureuses.Assurance de la qualité et essais
Des protocoles complets de test et d'assurance qualité font partie intégrante de la fabrication des RCCB. La validation en ligne comprend des essais à haut potentiel à 4kV AC pendant 60 secondes, une simulation de courant différentiel avec des applications de 0,5IΔn (15mA) et 1IΔn (30mA), et des essais d'endurance mécanique de 10 000 cycles opérationnels à un pouvoir de coupure de 6 000A. La certification finale du produit implique des bancs d'essai automatisés effectuant des analyses d'élévation de température, des essais de stress environnemental dans des conditions extrêmes et des vérifications de l'immunité CEM. Le contrôle statistique des processus maintient un Cpk ≥1,67 pendant les essais de production de 100% avec un échantillonnage supplémentaire de 0,65% NQA pour l'assurance de la qualité. La thermographie IR vérifie une élévation de température <50K à 1,13In, tandis que les tests d'immunité CEM comprennent une résistance aux surtensions de 8kV/15kV et une immunité aux champs RF de 10V/m. Les tests de stress environnemental comprennent 85°C/85% RH pendant 96 heures et la capacité de démarrage à froid à -25°C.Avantages de la fabrication chinoise
La domination de la Chine dans la fabrication de RCCB s'explique par son écosystème de fabrication avancé et ses investissements stratégiques dans l'automatisation. Le pays dispose d'un écosystème de pièces et de composants complet et rentable, qui offre des conditions inégalées pour la fabrication de produits électroniques. Cette chaîne d'approvisionnement intégrée permet de s'approvisionner rapidement en composants spécialisés, des écrans tactiles aux cartes de circuits imprimés, ce qui permet une production efficace et des ajustements rapides aux demandes du marché. Les usines chinoises ont adopté les technologies de l'industrie 4.0, en investissant massivement dans la robotique intelligente, les données du cloud et les lignes de production automatisées. Par exemple, la nouvelle ligne de production automatisée de disjoncteurs miniatures flexibles d'ABB à Pékin présente des principes avancés de l'industrie 5.0, intégrant la reconnaissance visuelle, la technologie d'alimentation flexible et les processus pilotés par l'IA. Cet accent mis sur l'automatisation et la numérisation a considérablement amélioré la stabilité, la flexibilité et l'efficacité de la fabrication tout en réduisant les coûts, ce qui permet aux fabricants chinois de produire des RCCB de haute qualité à des prix compétitifs.Avantages du RCCB de VIOX Electric
VIOX Electric se distingue en tant que premier fabricant de RCCB par son engagement en faveur de l'excellence technique, de la fiabilité des produits et de l'innovation axée sur le client. L'expertise en conception avancée de l'entreprise emploie des stratégies de conception pour la fabrication (DFM), optimisant les RCCB à la fois pour la performance et la fabricabilité. Leur approche de fabrication intelligente intègre des technologies de pointe telles que la simulation de jumeaux numériques et la traçabilité par blockchain, garantissant un contrôle qualité inégalé.Les principaux avantages du choix de VIOX Electric sont les suivants
- Capacités de certification multi-normes grâce à des installations d'essai internes accréditées ISO 17025.
- Fiabilité exceptionnelle avec Cpk ≥1,67 maintenue grâce aux tests de production du 100% et à un échantillonnage supplémentaire.
- Temps de réponse rapides, les modèles haut de gamme atteignant des temps de déclenchement de 10 ms grâce à des circuits magnétiques optimisés.
- Des systèmes de production flexibles capables de gérer 71 variantes techniques.
- Conceptions spécialisées à double tension (85-300V) avec détection automatique pour une compatibilité avec le marché mondial.
- Des pratiques de fabrication durables, y compris des processus de refroidissement en circuit fermé et de récupération de l'argent.
- Une assistance technique complète et une documentation transparente pour faciliter la mise en conformité avec la réglementation.
Demande d'un RCCB personnalisé
VIOX RCCB est heureux de vous aider à répondre à vos besoins en matière de RCCB OEM et Private Label. Nous fournissons des solutions qui sont à la fois de haute qualité et abordables.