Производитель Изоляторов Шинопроводов
VIOX является производителем изоляции шин для вашего бренда. Мы являемся самым быстрым и простым способом создания или продвижения вашего бренда с помощью высококачественной продукции.
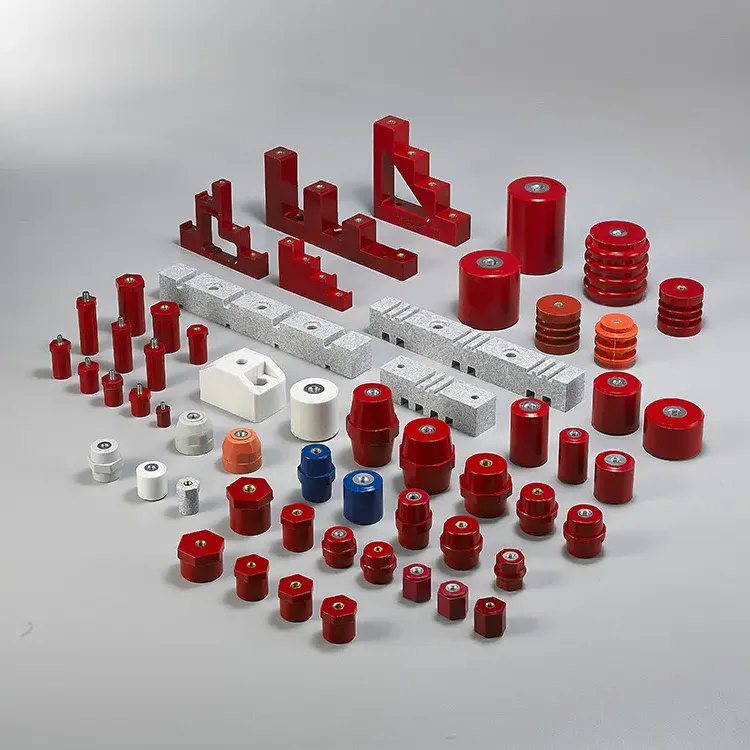
Изоляторы шин, критически важные компоненты систем распределения электроэнергии, изготавливаются с помощью специализированных процессов с использованием таких материалов, как сыпучий формовочный компаунд и ненасыщенные полимеры со стекловолокном, чтобы обеспечить надежную электрическую изоляцию и механическую поддержку.
Материалы для изоляторов сборных шин
Основными материалами, используемыми для производства шинных изоляторов, являются компаунд для объемного формования (BMC) и ненасыщенный полимер, армированный стекловолокном. Эти композитные материалы тщательно отбираются за их превосходное электрическое сопротивление, термостойкость и огнестойкость. Некоторые производители также используют фарфор или стекло в качестве диэлектрических материалов, в зависимости от конкретных требований к применению. Выбор материалов имеет решающее значение для обеспечения того, чтобы готовый продукт мог выдерживать механические нагрузки, связанные с поддержкой тяжелых шин, сохраняя при этом превосходные электроизоляционные свойства в различных условиях эксплуатации.
Процесс производства шинной изоляции
Процесс производства шинных изоляторов включает в себя несколько ключевых этапов, начиная с точной подготовки материала. Изоляционные материалы тщательно взвешиваются, чтобы обеспечить правильный состав и свойства. Затем процесс формовки проходит в определенной последовательности:
- Нагрев формы до соответствующей температуры
- Установка металлических вставок в форму при необходимости
- Добавление изоляционного материала в форму
- Закрытие формы для формирования изолятора
Для многослойных шинных изоляторов используется другой метод. Он предусматривает укладку чередующихся слоев проводников и изоляции с последующим начальным прессованием для скрепления слоев. Затем удаляются излишки материала и удерживающие выступы, после чего производится окончательное прессование для полной герметизации изоляции. На всех этапах производства осуществляется строгий контроль качества, чтобы конечный продукт соответствовал стандартам электробезопасности и эксплуатационным требованиям.
Основные характеристики качества
Процесс производства изоляторов для шин разработан таким образом, чтобы получить компоненты с особыми качественными характеристиками, необходимыми для обеспечения их производительности и надежности. Эти изоляторы имеют низкую усадку, что помогает сохранить стабильность размеров и предотвратить деформацию под нагрузкой. Кроме того, они обладают высоким электрическим сопротивлением, превосходной тепло- и огнестойкостью, а также водонепроницаемостью. Благодаря этим свойствам изоляторы могут эффективно поддерживать и изолировать шины в различных условиях окружающей среды, сохраняя их целостность в системах распределения электроэнергии. Сочетание этих свойств позволяет создать продукт, способный выдерживать жесткие условия эксплуатации, обеспечивая при этом надежную электрическую изоляцию и механическую поддержку.
Свойства материалов изоляторов
Готовые шинные изоляторы демонстрируют исключительную механическую прочность, способную выдержать значительный вес шин и подключенного к ним оборудования. Эти компоненты обладают превосходными электроизоляционными свойствами, что крайне важно для предотвращения пробоев в системах распределения электроэнергии. Материалы, используемые при их изготовлении, такие как компаунд для объемного формования (BMC) и ненасыщенные полимеры со стекловолокном, способствуют их долговечности в суровых условиях. Такое сочетание свойств обеспечивает надежную работу в различных условиях эксплуатации, что делает шинные изоляторы незаменимыми для поддержания безопасности и эффективности электрической инфраструктуры.
Преимущества партнерства с производителями
Работа со специализированными производителями шинных изоляторов дает значительные преимущества проектировщикам и операторам электрических систем. Эти производители предоставляют опыт в области индивидуальных решений, обеспечивая оптимальную производительность и экономическую эффективность для конкретных приложений. Сотрудничая с опытными производителями, вы можете получить следующие преимущества:
- Индивидуальные проекты, которые точно соответствуют требованиям проекта, сокращают количество отходов и исключают необходимость переделки.
- Доступ к высококачественным материалам, которые повышают долговечность и производительность, что позволяет сократить количество ремонтов и замен со временем
- Постоянное качество и потенциальная экономия средств благодаря долгосрочным партнерским отношениям
- Соответствие отраслевым стандартам и сертификатам, обеспечивающее надежность и безопасность
- Инновационные решения, повышающие эффективность системы, такие как многослойные шины, обеспечивающие меньшую индуктивность и большую токопроводящую способность
Сотрудничество с надежными производителями шинных изоляторов в конечном итоге приводит к повышению надежности электрических систем, снижению эксплуатационных расходов и улучшению общих результатов проекта.
Компромисс между качеством и стоимостью
Высококачественные шинные изоляторы имеют значительные преимущества перед низкокачественными аналогами в плане безопасности, надежности и долгосрочной рентабельности. Изоляторы премиум-класса обычно изготавливаются из высококачественных материалов, таких как эпоксидная смола или высококачественный фарфор, обеспечивающих превосходную электрическую прочность и термостойкость до 180°C. Эти свойства обеспечивают стабильную работу в сложных условиях, снижая риск возникновения электрических неисправностей и отказов системы.
В отличие от них, низкокачественные изоляторы часто страдают от дефектов материала, таких как микротрещины или воздушные пузыри, что может привести к преждевременным поломкам и утечке электричества. Кроме того, они могут не обладать необходимой гибкостью, что может привести к разрыву или размыванию при механическом воздействии во время установки или эксплуатации. Изначально более дешевые, некачественные изоляторы могут привести к увеличению затрат на обслуживание, более частым заменам и потенциальной угрозе безопасности, что в конечном итоге подрывает доверие к электрической системе и бренду, связанному с ней. Инвестиции в высококачественные шинные изоляторы имеют решающее значение для поддержания надежности системы, обеспечения соответствия требованиям безопасности и оптимизации долгосрочных эксплуатационных расходов.
Индивидуальные решения для повышения эффективности
Производители шинных изоляторов на заказ предлагают значительные преимущества в эффективности благодаря своему специализированному опыту и адаптированным производственным процессам. Эти производители используют такие передовые технологии, как 3D-печать для быстрого создания прототипов и прецизионные стальные правильные штампы для резки изоляции, что обеспечивает однородность и качество конечного продукта. Их способность быстро адаптировать дизайн с использованием большого количества пресс-форм позволяет сократить время выполнения заказа и уменьшить количество отходов, так как производится только необходимое количество продукции.
Эффективность повышается благодаря глубокому пониманию производителями свойств материалов и требований к их применению. Например, они могут рекомендовать оптимальные изоляционные материалы, такие как DMC, эпоксидные или полиолефиновые термоусадочные муфты, исходя из конкретных потребностей проекта, что повышает производительность и экономическую эффективность. Такой опыт в выборе материалов и их подгонке не только упрощает производственный процесс, но и приводит к созданию более надежных и долговечных решений по изоляции шин, что в конечном итоге снижает долгосрочные затраты и повышает эффективность системы для клиентов.
Разнообразные варианты изоляции
Производители изоляторов для сборных шин предлагают широкий выбор опций для удовлетворения различных требований к электрическим системам. Эти варианты включают различные изоляционные материалы, такие как эпоксидная смола, полиолефиновые термоусадочные муфты и ПВХ-покрытия, каждый из которых подходит для конкретных областей применения и условий окружающей среды. Производители могут адаптировать процесс изоляции к геометрии шинопровода, используя такие методы, как порошковое покрытие для сложных форм или термоусадочные трубки для гибких соединений.
Кроме того, производители по индивидуальному заказу предлагают выбор материала проводников, как правило, медь или алюминий, и варианты отделки, такие как оловянное, никелевое или серебряное покрытие для улучшения электрических свойств и коррозионной стойкости. Такая гибкость позволяет создавать оптимизированные решения, которые обеспечивают баланс между производительностью, стоимостью и конкретными потребностями проекта, обеспечивая эффективные и надежные системы распределения электроэнергии в различных отраслях промышленности.
Производители: Партнеры по процессу
Производители шинных изоляторов оказывают неоценимую поддержку на протяжении всего жизненного цикла проекта, от первоначального проектирования до установки и технического обслуживания. Их опыт помогает оптимизировать работу системы и снизить затраты на каждом этапе:
- Стадия проектирования: Производители предлагают технические консультации, чтобы помочь выбрать наиболее подходящие материалы и конфигурации изоляторов, исходя из конкретных требований к применению, уровням напряжения и условиям окружающей среды.
- Прототипирование: Возможности быстрого создания прототипов позволяют быстро проводить итерации и тестировать индивидуальные проекты до начала полномасштабного производства.
- Производство: Передовые производственные процессы обеспечивают стабильное качество и соблюдение жестких допусков, сводя к минимуму риск возникновения дефектов или отказов.
- Поддержка при установке: Производители часто предоставляют подробные инструкции по установке и техническую помощь на месте для обеспечения правильного применения.
- Послепродажное обслуживание: Постоянная поддержка включает в себя устранение неисправностей, рекомендации по техническому обслуживанию и запасные части для обеспечения максимальной долговечности и надежности систем изоляции шин.
Используя знания и ресурсы производителя на протяжении всего процесса, руководители проекта могут избежать дорогостоящих ошибок, повысить эффективность системы и обеспечить долгосрочную работу электротехнической инфраструктуры.
Опытные партнеры-производители
Опытные производители шинной изоляции привносят в производственный процесс десятилетия опыта, обеспечивая высокое качество продукции, отвечающей строгим отраслевым стандартам. Такие компании, как ASTA Group, имеющие более чем 200-летний опыт производства медных изолированных проводов, демонстрируют глубину знаний в этой области. Этот обширный опыт воплощается в передовых производственных технологиях, таких как специализированные технологии изоляции, разработанные для конкретных проектов, которые повышают производительность и безопасность продукции.
Производители с большим опытом работы часто имеют налаженные отношения с поставщиками и глубокое понимание свойств материалов, что приводит к повышению эффективности производства и улучшению контроля качества. Их опыт позволяет им ориентироваться в сложных нормативных требованиях, внедрять принципы бережливого производства и предоставлять ценные сведения о дизайне и оптимизации продукции. Этот богатый опыт в конечном итоге приводит к созданию более надежных, эффективных и экономически выгодных решений по изоляции шин для клиентов из различных отраслей промышленности.
Экологичные методы производства
Устойчивая производственная практика при изготовлении шинных изоляторов направлена на снижение воздействия на окружающую среду при сохранении качества продукции. Производители все чаще используют возобновляемые источники энергии, причем некоторые из них вырабатывают электроэнергию с помощью солнечных батарей и при необходимости дополняют ее зеленым газом и электричеством 100%. Такой переход на экологически чистую энергию значительно снижает углеродный след производственных процессов.
Также изучаются инновационные материалы и технологии для повышения устойчивости:
- Использование вторичного сырья и внедрение экологичных покрытий при производстве шин.
- Разработка электроники на основе дерева и бумаги для уменьшения количества электронных отходов.
- Внедрение технологий аддитивного производства, таких как 3D-печать, которые позволяют снизить воздействие на окружающую среду до 86% для гибких электронных компонентов.
- Внедрение технологий "умной фабрики" для мониторинга и оптимизации энергопотребления в режиме реального времени.
Такие методы не только способствуют сохранению окружающей среды, но и часто приводят к долгосрочной экономии средств и повышению эффективности продукции.
Китайское производственное преимущество
Китайские производители стали лидерами в отрасли шинных станков, предлагая ряд ключевых преимуществ:
- Экономическая эффективность: Станки для производства шин китайского производства отличаются конкурентоспособной ценой без ущерба для качества, что делает их привлекательными для предприятий по всему миру.
- Технологические инновации: Такие компании, как SunShine Busbar Machine Manufacturing Company, разработали уникальные запатентованные технологии, такие как модульная структурная конструкция и компенсация пружинного отката, повышающие точность обработки и эффективность производства.
- Универсальность: Китайские производители предлагают широкий ассортимент шинных станков, от портативных гидравлических моделей до полностью автоматизированных систем с ЧПУ, отвечающих различным производственным потребностям и бюджетам.
- Экспортный опыт: Многие китайские производители шинных станков прочно обосновались на международных рынках, особенно в Юго-Восточной Азии, на Ближнем Востоке, в Южной Америке и Африке.
- Возможности персонализации: Китайские производители часто предлагают индивидуальные решения для удовлетворения конкретных требований заказчика, обеспечивая оптимальную производительность для различных областей применения.
Благодаря этим преимуществам китайские производители шинных станков стали грозными конкурентами на мировом рынке, предлагая привлекательное сочетание доступности, инноваций и надежности.
Выбор надежных производителей
При поиске подходящего производителя шинных изоляторов учитывайте несколько ключевых факторов для обеспечения качества и надежности:
- Сертификаты: Ищите производителей с сертификатами ISO и соответствия отраслевым стандартам IEC и UL. Это свидетельствует о соблюдении процессов управления качеством и безопасности продукции.
- Опыт и знания: Известные производители с большим опытом работы в производстве шинных изоляторов с большей вероятностью предоставят высококачественную продукцию и ценную техническую поддержку.
- Возможность индивидуальной настройки: Выбирайте производителя, который предлагает индивидуальные решения для удовлетворения ваших конкретных требований к проекту, включая выбор материала, тип изоляции и конфигурацию шин.
- Производственные мощности: Убедитесь, что производитель может удовлетворить ваши потребности в объемах и сроках поставки без ущерба для качества.
- Отзывы покупателей: Изучите отзывы других клиентов, чтобы оценить надежность производителя, качество продукции и послепродажную поддержку.
- Техническая поддержка: Отдавайте предпочтение производителям, которые предоставляют всестороннюю помощь на протяжении всего жизненного цикла проекта, начиная с консультации по проектированию и заканчивая руководством по установке и техническим обслуживанием.
Тщательно оценив эти аспекты, вы сможете выбрать производителя шинных изоляторов, который наилучшим образом соответствует потребностям вашего проекта и ожиданиям качества.
Запрос на заказ Изоляторы шин OEM
Компания VIOX Busbar Insulators рада помочь вам с вашими требованиями к шинным изоляторам OEM и Private Label. Мы предлагаем высококачественные и доступные решения.