Modular Contactor Manufacturer
VIOX is A Modular Contactor Manufacturer for your Brand. We are the fastest ad easiest way to build or promoter your brand through high-quality production.
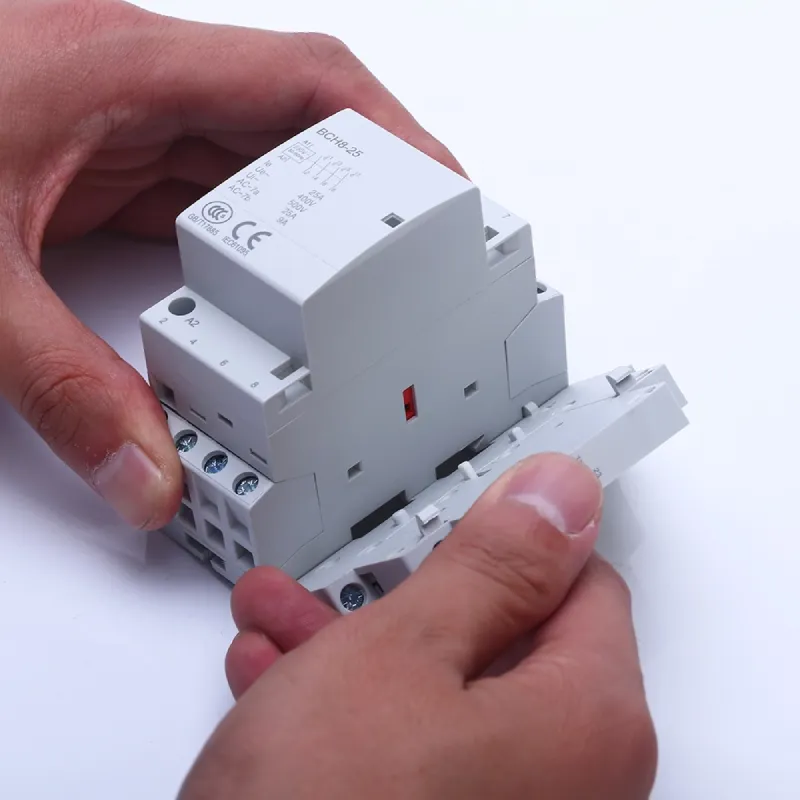
In today’s rapidly evolving electrical industry, modular contactors represent a fundamental component in power management systems. These devices, designed for controlling electrical circuits and equipment, have become increasingly sophisticated, offering enhanced functionality, reliability, and energy efficiency. This comprehensive guide explores the intricacies of modular contactor manufacturing, providing valuable insights for professionals seeking to understand the production process, material considerations, and key factors in selecting the right manufacturing partner.
Understanding Modular Contactors: Function and Applications
Modular contactors are electromechanical switching devices designed to establish or interrupt an electrical power circuit. Unlike traditional contactors, modular versions offer greater flexibility, simplified installation, and enhanced compatibility with modern electrical systems. They serve critical functions across various industries:
- Industrial automation systems requiring precise electrical control
- Building management for HVAC and lighting control
- Power distribution networks requiring reliable load switching
- Renewable energy systems needing efficient power management
- Motor control applications demanding consistent performance
As electrical systems continue to advance, the demand for high-quality, reliable modular contactors manufactured to exacting standards has grown substantially.
The Modular Contactor Manufacturing Process
The production of modular contactors involves a sophisticated multi-stage process that combines precision engineering with advanced quality control measures:
Design and Prototyping
The manufacturing journey begins with comprehensive design engineering, where specifications are established based on intended applications and performance requirements. Computer-aided design (CAD) software enables engineers to create precise 3D models, allowing for virtual testing and refinement before physical prototyping begins. This stage is crucial for ensuring the final product meets all electrical, mechanical, and thermal requirements.
Component Production
Once designs are finalized, the manufacturing of individual components commences. This includes:
- Contact points: Typically made from silver alloys or copper-tungsten composites for optimal conductivity and arc resistance
- Housing units: Precision-molded from engineering-grade polymers to ensure electrical insulation and mechanical durability
- Electromagnetic coils: Wound with precision to exact specifications for consistent operation
- Terminals and connectors: Manufactured to ensure reliable electrical connections and ease of installation
Each component undergoes rigorous quality testing before advancing to the assembly phase.
Assembly and Integration
Modern modular contactor assembly combines automated precision with skilled manual oversight. Advanced assembly lines utilize robotics for consistent component placement while experienced technicians handle quality verification. This hybrid approach ensures both production efficiency and meticulous attention to detail.
Testing and Certification
Perhaps the most critical phase in manufacturing is comprehensive testing. Quality manufacturers implement:
- Dielectric strength testing to verify insulation integrity
- Contact resistance measurement to ensure optimal electrical performance
- Mechanical endurance testing to confirm operational longevity
- Thermal performance evaluation to validate operation under temperature extremes
- Electromagnetic compatibility testing to ensure reliable performance in complex systems
Products that meet or exceed industry standards then receive appropriate certifications, such as CE, NF, Semko, ISI, UKCA, and SAA, verifying their compliance with international safety and performance requirements.
Types of Modular Contactors
Modular contactors are categorized based on several parameters, offering versatility for various applications:
- Number of Poles: Available in 1P, 2P, 3P, and 4P configurations, with 2P and 4P common for residential and industrial use
- Current Type: AC contactors for general use, with grid arc extinguishing, and DC contactors for battery systems, using magnetic arc suppression
- Application-Specific: General-purpose for lighting and heating, motor control for industrial motors, and specialized types like capacitor-switching contactors
- Operating Mode: Manual for direct operation, automatic for remote control, offering flexibility in building automation
- Contact Type: Normally open (NO) for standard switching, normally closed (NC) for safety circuits, with options for auxiliary contacts for signaling
Material Selection Options in Modular Contactor Manufacturing
The selection of appropriate materials dramatically influences the performance, reliability, and longevity of modular contactors. Premier manufacturers carefully consider several critical material decisions:
Contact Materials
The electrical contacts represent the heart of any contactor, directly influencing its performance and service life. Common options include:
- Silver-cadmium oxide (AgCdO): Traditionally offering excellent conductivity and arc-quenching properties, though being phased out due to environmental concerns
- Silver-tin oxide (AgSnO₂): Providing superior resistance to welding and material transfer, particularly suitable for high-inrush applications
- Silver-nickel (AgNi): Offering good electrical conductivity with improved wear resistance compared to pure silver
- Silver-graphite (AgC): Delivering self-lubricating properties that reduce wear in high-cycle applications
The optimal material selection depends on the intended application, with considerations for switching frequency, load characteristics, and environmental conditions.
Housing and Insulation Materials
Modern modular contactors utilize advanced polymer compounds for housing and insulation components:
- Glass-reinforced polyamide: Providing excellent electrical insulation with enhanced mechanical strength and dimensional stability
- Polycarbonate: Offering superior impact resistance and transparency for visual inspection
- Thermoplastic polyester: Delivering excellent chemical resistance and dimensional stability in challenging environments
These materials must provide appropriate electrical insulation properties while withstanding mechanical stress, thermal cycling, and potential exposure to chemicals or UV radiation.
Coil and Core Materials
The electromagnetic system driving contactor operation requires specialized materials:
- Copper wire with high-grade insulation for coil windings
- Silicon steel laminations for magnetic cores, optimized to reduce eddy current losses
- Advanced ferrite materials for enhanced magnetic efficiency in premium designs
Materials and Features: Advancing Contactor Performance
Beyond basic material selection, leading manufacturers implement specialized features that enhance performance and reliability:
Arc Suppression Technologies
Modern contactors incorporate sophisticated arc suppression mechanisms:
- Arc chambers with splitter plates to extend and cool the arc
- Magnetic blow-out systems that use magnetic fields to elongate and extinguish arcs
- Advanced contact geometries that facilitate arc movement away from contact surfaces
These technologies significantly extend contactor lifespan by minimizing contact erosion during switching operations.
Enhanced Terminal Designs
Advanced terminal configurations improve installation efficiency and connection reliability:
- Cage clamp technology for secure wire retention without periodic retightening
- Multi-conductor terminals accommodating various wire sizes and types
- Touch-safe designs reducing risk of accidental contact with live parts
Modular Expansion Capabilities
Premium contactors offer extensive modularity through:
- Auxiliary contact blocks that snap onto the base contactor
- Mechanical interlocks for implementing mutual exclusion logic
- Timer modules for implementing delayed operations
- Electronic monitoring interfaces enabling integration with control systems
Technical Considerations in Modular Contactor Design
The engineering of high-performance modular contactors involves numerous technical considerations that influence their functionality and reliability:
Electrical Ratings and Parameters
Critical electrical specifications include:
- Operational voltage range (typically 24-690V AC/DC)
- Current handling capacity (from 6A to 100A or more)
- Making and breaking capacity under various load conditions
- Short-circuit withstand ratings
- Insulation voltage and impulse withstand levels
Mechanical Durability
Physical robustness is essential for long-term reliability:
- Mechanical operation cycles (typically 1-10 million operations)
- Contact wear resistance under various load conditions
- Vibration and shock resistance per IEC standards
- Terminal torque specifications for secure connections
Environmental Considerations
Modern contactors must perform reliably across diverse operating conditions:
- Operating temperature range (typically -25°C to +60°C)
- Humidity tolerance (up to 95% non-condensing)
- Altitude derating factors for installations above 2000m
- Pollution degree ratings for various installation environments
Flexible Manufacturing Solutions
Leading modular contactor manufacturers implement flexible production methodologies that balance efficiency with customization capabilities:
Automated Production Lines
State-of-the-art manufacturing facilities utilize:
- High-precision robotics for consistent component placement
- Automated optical inspection systems for real-time quality verification
- Advanced testing equipment integrated directly into production lines
These automated systems ensure consistent quality while maintaining efficient production rates.
Customization Capabilities
Premium manufacturers maintain flexibility to address specialized requirements:
- Custom coil voltages for specific control system compatibility
- Modified terminal configurations for unique installation requirements
- Special contact materials for challenging applications
- Custom marking and labeling for improved system documentation
Just-in-Time Manufacturing
Efficient production planning enables:
- Reduced inventory costs through optimized production scheduling
- Faster response to market demands with flexible manufacturing cells
- Enhanced quality control through streamlined production flow
Eco-Friendly Modular Contactor Production
Environmental responsibility has become increasingly important in manufacturing operations, with leading producers implementing sustainable practices:
RoHS and REACH Compliance
Modern contactors comply with international environmental regulations:
- Elimination of hazardous substances such as lead, mercury, and cadmium
- Documentation of chemical constituents ensuring regulatory compliance
- Material traceability systems for verification and auditing
Energy-Efficient Manufacturing
Sustainable production practices include:
- Energy-efficient machinery reducing carbon footprint
- Waste heat recovery systems improving overall efficiency
- Optimized production scheduling minimizing energy consumption
Waste Reduction Initiatives
Responsible manufacturers implement:
- Material recycling programs for production waste
- Reduced packaging waste through optimized designs
- Water conservation measures in manufacturing processes
The Chinese Manufacturing Edge in Modular Contactors
China has emerged as a global leader in electrical component manufacturing, offering several significant advantages:
Manufacturing Infrastructure
China’s robust electrical manufacturing ecosystem provides:
- Comprehensive supply chains reducing production costs and lead times
- Advanced production facilities incorporating cutting-edge technologies
- Specialized manufacturing clusters fostering innovation and efficiency
Technical Expertise
Chinese manufacturers have developed substantial capabilities:
- Experienced engineering teams with specialized knowledge
- Advanced R&D facilities driving continuous improvement
- Technical collaboration with international standards organizations
Cost-Effectiveness
Competitive advantages include:
- Economies of scale through optimized production volumes
- Efficient logistics networks for global distribution
- Strategic investment in automation balancing cost and quality
Selecting Your Modular Contactor Manufacturing Partner
Choosing the right manufacturing partner involves careful evaluation of several key factors:
Quality Certification and Standards
Reputable manufacturers maintain comprehensive certifications:
- ISO 9001 quality management systems
- Product-specific certifications like CE, NF, Semko, ISI, UKCA, and SAA
- UL and CSA listings for North American markets
- IEC compliance documentation for international acceptance
Technical Support Capabilities
Valuable manufacturing partners provide:
- Application engineering assistance for optimal product selection
- Technical documentation in multiple languages
- Troubleshooting support for installed products
- Training resources for installation and maintenance personnel
Manufacturing Flexibility
Effective partners offer:
- Scalable production capacity accommodating varying order volumes
- Quick-turn prototyping for new applications
- Customization options addressing specific requirements
- Flexible minimum order quantities for specialized products
Why Choose VIOX as Your Modular Contactor Manufacturer
VIOX has established itself as a premier modular contactor manufacturer, offering distinct advantages:
Comprehensive Certification Portfolio
VIOX products carry extensive international certifications, including CE, NF, Semko, ISI, UKCA, and SAA, ensuring compliance with global standards and facilitating worldwide acceptance.
Advanced Manufacturing Facilities
Our state-of-the-art production facilities incorporate:
- Automated assembly systems ensuring consistent quality
- Comprehensive testing laboratories verifying performance specifications
- Flexible manufacturing cells accommodating customization requirements
Technical Excellence
VIOX engineering teams deliver:
- Innovative product designs addressing evolving market needs
- Rigorous quality control processes exceeding industry standards
- Continuous improvement initiatives driving product advancement
Customer-Focused Approach
We prioritize customer satisfaction through:
- Responsive technical support addressing application questions
- Reliable delivery schedules supporting production planning
- Comprehensive documentation facilitating installation and maintenance
- Collaborative problem-solving for challenging applications
Conclusion
The selection of a modular contactor manufacturer represents a significant decision affecting system reliability, performance, and cost-effectiveness. By understanding the manufacturing processes, material considerations, and technical specifications outlined in this guide, electrical professionals can make informed decisions that optimize their power control systems.
VIOX stands ready to serve as your trusted partner in modular contactor supply, offering the perfect combination of technical excellence, manufacturing capability, and customer support. Our comprehensive certification portfolio, including CE, NF, Semko, ISI, UKCA, and SAA, demonstrates our commitment to quality and compliance with international standards.
For more information on VIOX modular contactors and our manufacturing capabilities, please contact our technical support team or visit our product showcase.
Request a Custom OEM Modular Contactors
VIOX Modular Contactor is happy to assist you with your OEM and Private Label Modular Contactors requirements. We provide solutions that are both high-quality and affordable.